What is Porosity in Welding: Recognizing Its Causes and Enhancing Your Abilities
What is Porosity in Welding: Recognizing Its Causes and Enhancing Your Abilities
Blog Article
Porosity in Welding: Identifying Common Issues and Implementing Ideal Practices for Prevention
Porosity in welding is a pervasive concern that often goes undetected up until it creates significant troubles with the honesty of welds. This typical problem can endanger the stamina and sturdiness of welded structures, positioning security dangers and causing expensive rework. By recognizing the source of porosity and implementing efficient avoidance strategies, welders can considerably boost the quality and integrity of their welds. In this conversation, we will certainly check out the crucial factors adding to porosity formation, analyze its damaging impacts on weld efficiency, and discuss the best practices that can be taken on to decrease porosity event in welding processes.
Typical Root Causes Of Porosity
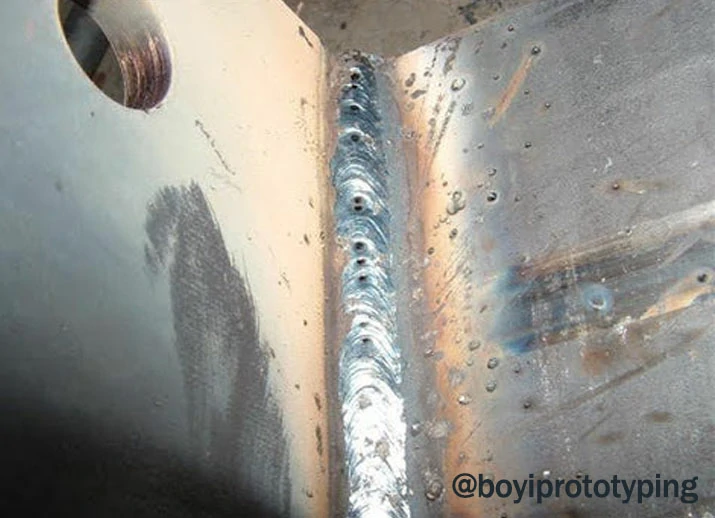
Using unclean or wet filler materials can introduce impurities right into the weld, adding to porosity issues. To alleviate these typical reasons of porosity, complete cleansing of base metals, proper protecting gas option, and adherence to optimal welding criteria are important techniques in attaining premium, porosity-free welds.
Effect of Porosity on Weld Quality

The existence of porosity in welding can substantially jeopardize the structural integrity and mechanical buildings of bonded joints. Porosity produces gaps within the weld steel, damaging its total strength and load-bearing ability.
Among the primary repercussions of porosity is a decline in the weld's ductility and strength. Welds with high porosity degrees often tend to exhibit lower influence strength and minimized ability to deform plastically before fracturing. This can be specifically concerning in applications where the bonded parts undergo dynamic or cyclic his response loading problems. Porosity can hamper the weld's ability to properly transmit pressures, leading to premature weld failing and possible security dangers in essential structures. What is Porosity.
Ideal Practices for Porosity Avoidance
To boost the structural honesty and top quality of bonded joints, what particular procedures can be implemented to minimize the incident of porosity throughout the welding procedure? Utilizing the correct welding technique for the specific material being bonded, such as readjusting the welding angle and gun position, can better prevent porosity. Normal evaluation of welds and immediate removal of any type of problems identified during the welding process are vital techniques to stop porosity and create high-grade welds.
Relevance of Appropriate Welding Methods
Carrying out proper welding methods is extremely more tips here important in guaranteeing the structural integrity and top quality of bonded joints, developing upon the foundation of effective porosity prevention measures. Excessive warmth can lead to increased porosity due to the entrapment of gases in the weld swimming pool. Furthermore, using the ideal welding specifications, such as voltage, current, and travel rate, is important for achieving sound welds with minimal porosity.
In addition, the choice of welding process, whether it be MIG, TIG, or stick welding, ought to align with the details needs of the job to ensure optimum results. Correct cleansing and prep work of the base metal, as well as picking the appropriate filler material, are likewise important elements of efficient welding techniques. By sticking to these ideal methods, welders can lessen the danger of porosity development and generate high-grade, structurally sound welds.
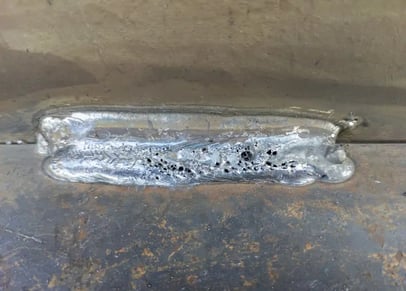
Examining and Quality Assurance Measures
Examining procedures are vital to detect and avoid porosity in welding, making certain the toughness and toughness of the last item. Non-destructive testing techniques such as ultrasonic screening, radiographic testing, and visual examination are generally employed to recognize potential issues like porosity.
Conducting pre-weld and post-weld inspections is likewise essential in preserving high quality click now control requirements. Pre-weld examinations entail verifying the products, tools settings, and cleanliness of the workspace to prevent contamination. Post-weld evaluations, on the other hand, analyze the final weld for any type of issues, consisting of porosity, and validate that it fulfills specified standards. Implementing a detailed quality assurance plan that includes detailed screening procedures and examinations is critical to decreasing porosity issues and guaranteeing the total high quality of welded joints.
Final Thought
In final thought, porosity in welding can be a typical problem that impacts the high quality of welds. By identifying the typical sources of porosity and carrying out ideal techniques for avoidance, such as appropriate welding strategies and screening actions, welders can make certain premium quality and reputable welds. It is vital to focus on avoidance approaches to decrease the occurrence of porosity and preserve the honesty of welded structures.
Report this page